- Home
- Knowledge Hub
- Structural Adhesives
- Your guide to MMA structural adhesives
Your guide to MMA structural adhesives
Scott Bader’s range of Crestabond MMA primerless structural adhesives are specifically designed to bond various substrates with minimal preparation needed and no requirement for primer, dramatically enhancing production efficiency and reducing costs and waste.
Here we delve into the key features and advantages of MMA structural adhesives vs other technologies available on the market today.
What are MMA structural adhesives?
A structural adhesive is generally classified as an adhesive that will cure to bond two substrates together and, in doing so, effectively becomes an integral part of the structure itself. It is not only an interface between the two substrates to be bonded, but it actively increases the strength, toughness and durability of the structure.
There are slightly different opinions but broadly speaking, a structural adhesive will cure to give a strength of at least 10MPa.
They are based on methyl methacrylate technology, often shortened to MMA.
MMAs have been widely used for a decade or so, therefore they are not as well established as their two main competing technologies; polyurethane and epoxy based structural adhesives.
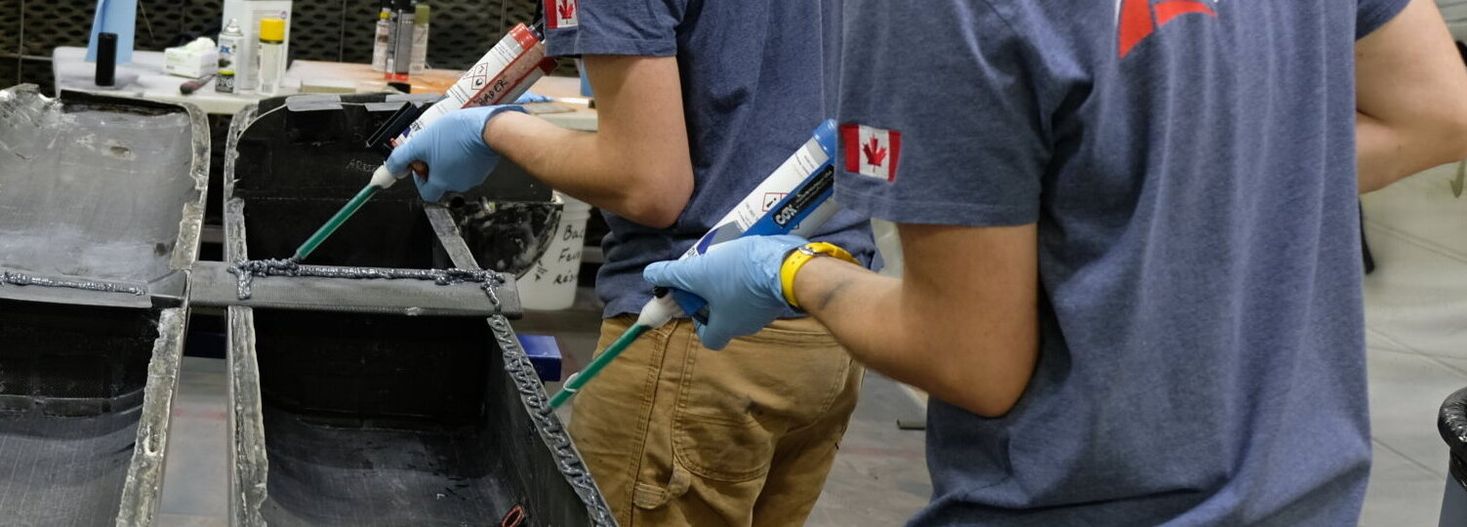
MMAs vs epoxy and polyurethane adhesives
Comparing MMA adhesives to the two other main types of structural adhesives, polyurethanes and epoxies, places them in the middle for mechanical properties. Whilst polyurethanes are well known for their flexibility, they often exhibit a low strength profile. The opposite can be said for epoxy adhesives; they show exceptional strength but at the cost of reduced flexibility.
MMA structural adhesives ultimately display properties that combine strength and flexibility.
They are two-part systems, meaning they are required to mix two components together before use. At Scott Bader, they are referred to as “adhesive” and “activator”. Once mixed, the adhesive must be applied within a designated “working time” before it starts to cure. If applied outside of this time, the adhesive may have partially cured and not be able to “wet out” the surfaces to give an adequate bond. The mix ratio between the two components also has a pronounced effect on the final properties of the cured adhesive.
The benefits
MMA structural adhesives offer incredible performance. Their reputation is built on the strength, toughness, gap filling and flexibility they offer.
Flexibility is a particularly sought after feature as typical users are often bonding dissimilar substrates such as metal to GRP. This is because dissimilar materials will have different coefficients of expansion in operation, so you need an adhesive that is sufficiently flexible to account for this.
Scott Bader’s Crestabond range bonds composites, metals and plastics including difficult to bond PP, PE and TPO.
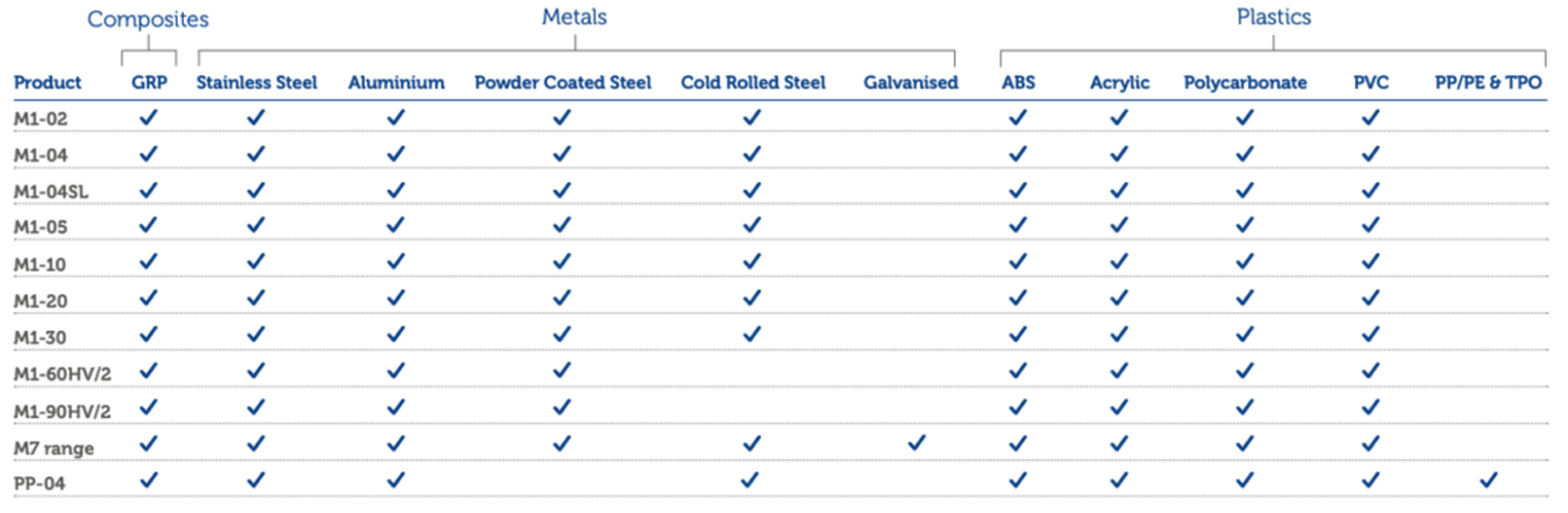
MMA adhesive technology is also versatile. Various physical/handling properties such as the viscosity, specific gravity, working time and even the colour can be manipulated in the formulation whilst still maintaining optimal structural properties. This means that, whilst there are limitations, it is possible to formulate MMA adhesives to meet the demands of a wide range of markets and applications. For this reason, MMA adhesives are commonly used in the marine, land transport, construction, renewable energy, electric vehicles and electronics markets, amongst others.
Comparing with other technologies
Welding
MMAs are cheaper, less labour-intensive and easier to use. They also offer a better aesthetic finish and can be sanded down to further improve the aesthetic. You are often also limited on the materials which can be joined by welding.
Mechanical fasteners
In comparison with mechanical fasteners, MMAs offer significant benefits. They are lighter, corrosion resistant, can be used in difficult to access areas, less labour intensive, more durable and they offer even distribution of strength across the bonded area.
Using a mechanical fastening such as a screw or bolt would require or facilitate the creation of a hole in the substrates to be bonded. This hole is not only a possible point of ingress for moisture or dust, for example, but it also introduces a weak spot as it is a stress concentration point.
Related

Storing and handling adhesives
Storage and handling recommendations for Scott Bader’s adhesives range.
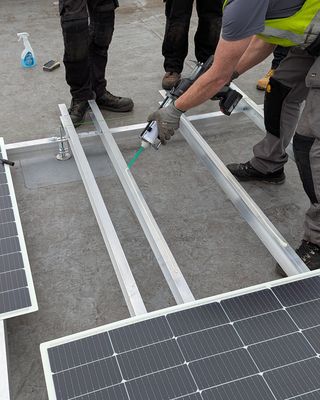
The advantages of structural adhesives
Structural adhesives negate the need to use mechanical fixings such as screws or bolts. These joining methods often require an additional production step of drilling a hole that creates a weakness in...
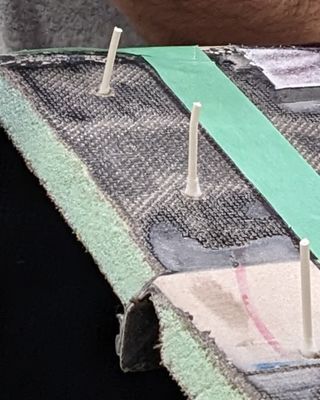
Applying structural adhesives
Although some adhesives are single component and can cure by other mechanisms such as heat or UV, Scott Bader’s Crestabond and Crestomer structural adhesives are two-component and cure by a process...
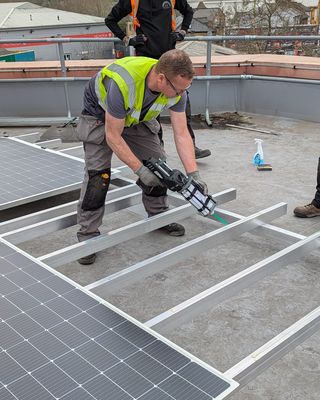
How structural adhesives are revolutionising solar PV installation
We recently caught up with Scott Bader’s solar PV expert, Andrew Harvey, on the improvements structural adhesives bring to solar installation, and how they should be used for optimum installation.